When it comes to transporting and storing medical supplies, nothing is more critical than ensuring products remain within precise temperature ranges. These goods—ranging from vaccines and biologics to diagnostic kits—require highly specialized handling and facilities. For companies that lack internal infrastructure, relying on third-party logistics for cold chain management is not only practical but often essential. However, not all logistics partners offer the same standards of quality or compliance.
Choosing a 3PL with top-tier temperature controlled storage capabilities can make the difference between preserving product efficacy and compromising patient safety. Here’s how healthcare and pharmaceutical companies can identify whether a 3PL partner offers the best in cold storage logistics solutions.
Table of Contents
Key Takeaways
✔ A reliable 3PL must offer multiple validated temperature zones, backups, and facility design built for medical-grade logistics. ✔ Continuous temperature tracking, alerts, and remote visibility are essential to prevent excursions and meet compliance standards. ✔ Validated packaging, compliant labeling, and fast, accurate shipping are critical to maintaining cold chain integrity. ✔ The 3PL must hold certifications like FDA, ISO 13485, and follow GDP, DSCSA, and other industry regulations. ✔ Choose a 3PL that can scale operations and offer customized services to match your changing business needs. ✔ Physical security, documented chain-of-custody, and disaster recovery plans are vital for protecting high-value medical products. ✔ Work with a 3PL that specializes in healthcare or pharmaceuticals and has a proven track record with similar clients. ✔ Transparency, regular updates, and responsive customer service are key to managing sensitive supply chains. ✔ Visiting the 3PL facility helps confirm operational readiness, infrastructure quality, and staff competency |
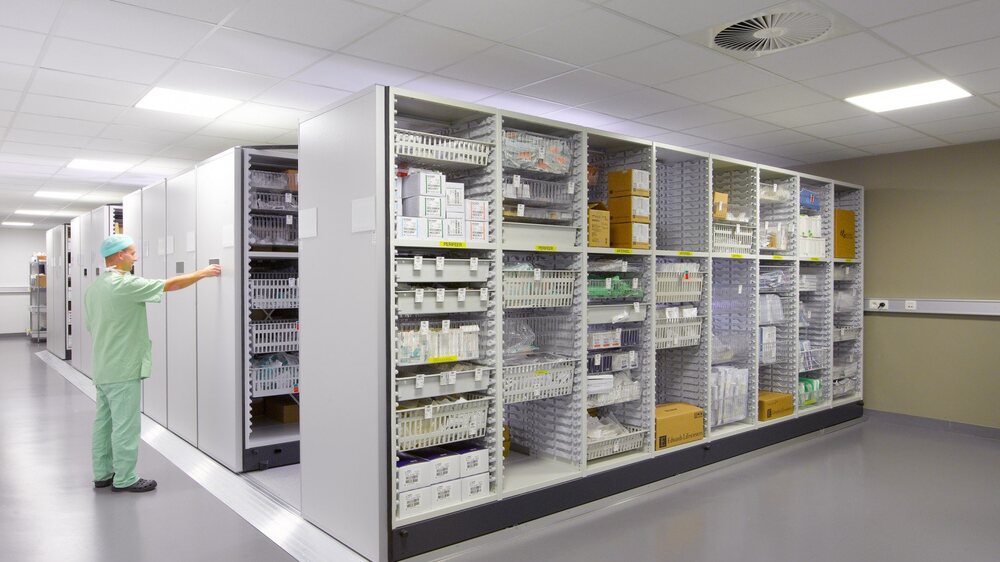
Understand the Unique Storage Needs of Medical Supplies
Medical supplies are not a one-size-fits-all category. Different products require specific storage conditions that, if not strictly maintained, can lead to product degradation, safety risks, and regulatory violations.
Temperature sensitivity varies by product
- Vaccines must be kept between 2°C and 8°C to remain effective.
- Biologics often require freezing at -20°C.
- Gene therapies and cell-based treatments may need ultra-low storage below -80°C.
- IV fluids, insulin, and diagnostic reagents also have narrow temperature tolerances.
Time and temperature exposure matter
Short-term exposure to temperatures outside acceptable ranges can be just as harmful as long-term improper storage. Even minutes of temperature excursion during transit or handling can reduce a product’s potency or safety. In fact, up to 35% of vaccines are damaged globally due to improper storage and handling, particularly in transit. This highlights how vulnerable these products are and the importance of precision throughout the supply chain.
Humidity control and light sensitivity
Some products are not just temperature-sensitive but also reactive to moisture and light. Advanced cold storage logistics solutions must offer environments with controlled humidity and light-blocking features when needed.
Shelf life and potency concerns
Temperature fluctuations can drastically shorten shelf life, especially for biologics and vaccines. A product that appears intact can lose potency silently, leading to ineffective treatment or misdiagnosis.
Regulatory complexity
Agencies like the FDA, WHO, and EMA expect strict adherence to Good Distribution Practice (GDP). Products must remain within labeled storage conditions from the point of manufacture to administration.
Evaluate the 3PL’s Cold Chain Infrastructure
The quality of a 3PL’s cold chain infrastructure directly determines its ability to store and transport temperature-sensitive products without risk. Medical-grade logistics demand far more than basic refrigeration. Choosing a 3PL with purpose-built infrastructure for refrigerated warehousing for perishable goods ensures that medical products are consistently stored under the right conditions, every step of the way.
Multiple validated temperature zones
Facilities should offer distinct, monitored storage environments:
- Refrigerated (2°C–8°C)
- Frozen (-20°C)
- Ultra-low (-80°C and below)
- Ambient controlled (15°C–25°C) for products that can’t tolerate extreme cold but still require stability
Redundant systems
Reliable cold storage logistics solutions must include fail-safes:
- Backup generators for uninterrupted power
- Dual refrigeration compressors to prevent total failure
- Environmental alarms that notify staff before excursions occur
Staging and buffer zones
Advanced facilities use pre-cooled staging areas to prevent temperature shock during loading and unloading. These transition zones help maintain the integrity of refrigerated warehousing for perishable goods during high-traffic periods.
Validated equipment and calibration
All refrigeration and monitoring equipment must be routinely validated and calibrated to meet audit standards and ensure precise operation.
GDP-compliant layout and design
Facilities purpose-built for medical cold storage will separate temperature zones, limit cross-contamination risks, and have cleanroom features where applicable. A well-designed facility reduces operational risks and enhances compliance.
Confirm Real-Time Temperature Monitoring and Alerts
Temperature controlled storage is only effective when there is full visibility and constant oversight. Passive systems or manual checks are no longer sufficient in today’s high-stakes regulatory environment. A reliable third-party logistics for cold chain management partner invests in technology that not only monitors but helps prevent problems, ensuring full visibility and accountability throughout the supply chain.
24/7 digital monitoring
The 3PL should use advanced sensors and data loggers that continuously track storage conditions in real time. Systems must monitor:
- Temperature
- Humidity (when applicable)
- Door open/close events
- Power interruptions
Instant alert systems
Immediate notifications via SMS, email, or platform alerts ensure staff can respond to any deviation within minutes. This helps protect product integrity and avoid costly product loss. A survey found that 20% of temperature-sensitive healthcare products are damaged during transport due to broken cold chains—making real-time alerts not just a benefit, but a necessity.
Automated audit trails and historical logs
For regulatory compliance, systems must store temperature records in a secure, retrievable format:
- PDF or CSV exports for inspections
- Timestamped logs with equipment ID and staff response details
- Integration with quality management systems (QMS)
Remote visibility dashboards
Clients benefit from online access to live dashboards where they can:
- Monitor current conditions
- Track shipments in transit
- View excursion reports
- Review the historical performance of 3PL supply chain solutions for sensitive goods
Compliance with global standards
Systems should align with guidelines such as:
- 21 CFR Part 11 (electronic records)
- WHO TRS 961
- USP <1079> for storage and transportation of drug products
Ask About Packaging, Labeling, and Fulfillment Capabilities
Temperature controlled storage alone is not enough to ensure cold chain success. The processes that happen outside the warehouse—especially packaging, labeling, and order fulfillment—are just as crucial for maintaining product integrity.
Use validated temperature-sensitive packaging
The 3PL must offer packaging solutions that have been rigorously tested and validated to maintain specific temperature ranges for the required duration. Examples include:
- Insulated shippers for short-haul refrigerated transport
- Phase-change materials and gel packs for extended cooling
- Dry ice for ultra-low temperature products
- Tamper-evident seals to ensure product security
Offer preconditioning and staging services
Products and packaging components should be preconditioned to the appropriate temperature before assembly. This minimizes the risk of thermal shock and helps preserve efficacy.
Ensure compliant, accurate labeling
Medical products require specific label information for safe and legal transport:
- Temperature requirements
- Hazard and handling warnings
- Barcodes and serial tracking per DSCSA or EU FMD
- Multilingual labels for international shipments
Support product traceability in fulfillment workflows
Fulfillment should include item-level tracking with serial number capture, batch numbers, and expiration dates to meet stringent recall and reporting requirements.
Maintain speed and accuracy in shipping
Delays in the pick-pack-ship process can allow products to fall outside their safe temperature range. Look for:
- Automated fulfillment workflows
- Controlled temperature zones during order assembly
- Fast turnaround to minimize dwell time outside refrigeration
Provide end-to-end cold chain integrity
A 3PL offering complete third-party logistics for cold chain management will ensure product safety from inbound receipt through final delivery, not just while sitting in storage.
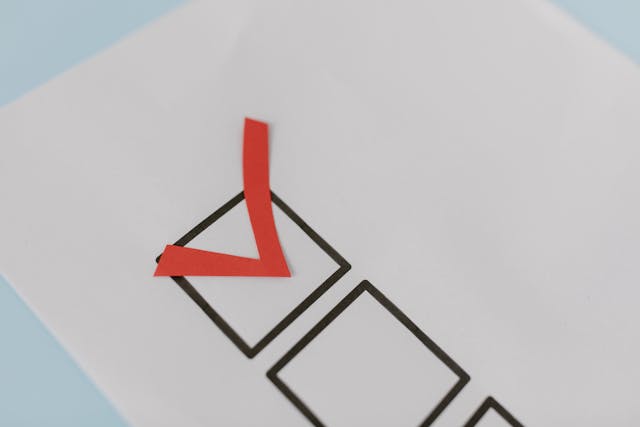
Assess the 3PL’s Regulatory Compliance and Certifications
In medical logistics, regulatory compliance is non-negotiable. Working with a certified 3PL ensures your company stays in alignment with legal and quality expectations.
Confirm essential certifications and licenses
A reliable 3PL should hold:
- FDA registration for handling and storing medical products
- State pharmaceutical licenses covering controlled or prescription goods
- ISO 13485 certification, demonstrating quality systems specific to medical devices
Check compliance with international standards
For companies operating globally, the 3PL should comply with:
- Good Distribution Practices (GDP) as outlined by the EU and WHO
- USP <1079> standards for pharmaceutical storage and transport
- PIC/S guidance, applicable to regulated international markets
Require DSCSA readiness
For U.S. distribution, the Drug Supply Chain Security Act requires:
- Serialized product traceability
- Transaction history and documentation
- Notification protocols for suspicious or illegitimate products
Request audit records and QMS documentation
Providers of cold storage logistics solutions should be transparent with:
- Results from past internal and third-party audits
- Standard Operating Procedures (SOPs)
- Corrective and Preventive Action (CAPA) logs
- Temperature excursion response protocols
Explore Customization and Scalability Options
Healthcare and pharmaceutical supply chains are dynamic. A capable 3PL must offer scalable and customizable solutions that align with changing business needs without compromising temperature control.
Adapt to fluctuating volumes
Seasonal demand shifts, clinical trial phases, or pandemic responses may require rapid capacity expansion or downsizing. Your 3PL should:
- Add cold storage space on demand
- Ramp up fulfillment staff and operations during spikes
- Scale down gracefully without penalty or service disruption
Offer service customization
Not all businesses need the same features. Tailored cold storage logistics solutions should include:
- Custom kitting for sample packs or clinical kits
- Label changes and relabeling services
- Return logistics and reverse cold chain handling
Support global and regional shipping models
Whether you’re shipping internationally or regionally, the 3PL should:
- Use packaging that meets international cold chain regulations
- Offer bonded warehouse services when needed
- Navigate import/export restrictions for perishable goods
Enable multi-temperature product handling
Some companies distribute products with varying storage requirements. The provider must offer:
- Segmented storage zones in the same facility
- Packaging options that preserve multiple temperature ranges in a single shipment
- Dedicated workflows for handling dual-temperature orders
Provide robust forecasting and planning support
Advanced 3PL supply chain solutions for sensitive goods will help clients:
- Predict storage needs using historical order data
- Align inventory cycles with expiration tracking
- Adjust safety stock levels for specialty or high-demand products
Prioritize Security and Risk Mitigation Strategies
Beyond temperature sensitivity, many medical supplies are also expensive, regulated, and at risk for diversion or tampering. A reliable 3PL must implement layered security and proactive risk controls to protect both the product and the client’s reputation.
Implement multi-layered physical security
A high-quality 3PL facility should feature:
- 24/7 video surveillance with monitoring and retention of footage
- Controlled access with keycard entry or biometric scanners
- Visitor logs and escort policies to prevent unauthorized access
- Motion detection systems for low-traffic or off-hours monitoring
Maintain strict chain-of-custody controls
Every touchpoint in the product journey should be documented. This includes:
- Inbound receiving logs
- Transfer tracking between zones or departments
- Detailed shipping records with courier handoff timestamps
Enforce staff screening and training protocols
Security starts with personnel. Ensure the 3PL:
- Conducts background checks and drug screenings
- Trains staff on handling sensitive medical products
- Maintains SOPs for product security and integrity
Develop and test disaster recovery plans
The 3PL should be prepared for emergencies such as:
- Power outages
- Equipment malfunctions
- Natural disasters (flood, fire, etc.)
Maintain comprehensive insurance coverage
Verify that the provider offers insurance for loss, damage, or temperature excursion events—protecting both the products and the financial interests of the client.
Choose a Partner with Industry Expertise
Not all logistics providers are equipped to handle medical-grade operations. The ideal partner should bring years of hands-on experience in cold chain environments specific to healthcare, pharmaceuticals, or biotech.
Select a vertical-specific 3PL
Providers focused on healthcare logistics understand:
- Industry-specific regulations and audit expectations
- Best practices for handling temperature controlled storage
- Requirements for specialty packaging and traceability
Review track record and client portfolio
Ask for:
- References from clients in similar sectors
- Case studies demonstrating successful cold chain implementations
- Problem-resolution examples that highlight how the provider mitigated supply chain issues
Gauge industry engagement and knowledge
An experienced 3PL should:
- Stay up to date with FDA, DSCSA, GDP, and USP guidelines
- Participate in industry forums or trade associations
- Offer insights on how evolving regulations affect logistics strategy
Look for Transparent Communication and Customer Support
A 3PL partnership must operate on trust, and that trust is built through transparency and responsiveness. Clear communication is especially critical in the fast-moving world of sensitive medical logistics. Transparent third-party logistics for cold chain management is not just about reporting data—it’s about fostering collaboration, accountability, and long-term success.
Ensure proactive status updates
Look for a 3PL that provides:
- Automatic shipment notifications
- Regular inventory status reports
- Alerts for delays or deviations—before they become problems
Request dedicated support
The best cold storage logistics solutions include:
- An assigned account manager or operations lead
- Direct access to support teams via phone, email, or dashboard
- Defined service level agreements (SLAs) for issue resolution
Review communication procedures during incidents
Ask how the 3PL handles:
- Temperature excursions or security breaches
- Product recalls
- Last-minute changes to delivery or inventory plans
Conduct a Site Visit Before Committing
Due diligence is critical when selecting a logistics partner. A site visit allows companies to confirm that claims match reality and assess the environment their products will rely on. A physical audit of the provider’s temperature controlled storage environment gives stakeholders the clarity and confidence needed to proceed with a partnership.
Inspect storage areas and infrastructure
During the tour, verify:
- Cleanliness and organization
- Clearly marked temperature zones
- Calibrated equipment and backup systems
Evaluate technology and monitoring systems
Ask to see:
- Real-time dashboards used for monitoring
- Historical temperature logs
- Alarm and alert test procedures
Review quality control documentation
Request to view:
- SOPs for handling medical supplies
- Staff training manuals
- Internal audit logs or compliance reports
Speak with the facility staff
Frontline employees offer insight into the actual day-to-day processes. Look for:
- Knowledge of proper product handling
- Familiarity with security and quality protocols
- Consistency in how procedures are followed
Frequently Asked Questions
What is the difference between temperature-controlled and climate-controlled storage?
Temperature-controlled storage maintains a consistent temperature to protect sensitive items from heat or cold. Climate-controlled storage, on the other hand, regulates both temperature and humidity. This is critical for products that are sensitive to moisture, such as diagnostic test kits, some antibiotics, and medical packaging materials that can degrade or become contaminated in high-humidity environments.
Why is humidity control important in storage facilities?
Humidity control helps prevent mold, mildew, corrosion, and warping in stored items. Excess moisture can damage packaging, labels, and the products themselves. This is especially important for pharmaceuticals, electronics, and paper-based goods.
Which medical products require temperature and humidity-controlled environments?
Certain medical products such as vaccines, insulin, intravenous fluids, blood products, and some diagnostic reagents require strict temperature and humidity control to maintain their safety and effectiveness. Exposure to heat, cold, or excess moisture can degrade these products, rendering them ineffective or even dangerous. Temperature-controlled storage ensures these sensitive items remain within their required stability range during storage and transit.
Are there different sizes of temperature-controlled storage units available?
Yes, temperature-controlled storage is available in various unit sizes to accommodate different needs. Small units may be used for documents or samples, while large units can hold pallets, equipment, or bulk pharmaceutical inventory. Choosing the right size depends on volume, packaging, and handling requirements.
How do temperature-controlled storage units maintain consistent conditions?
These units use specialized HVAC systems, insulation, and monitoring technology to maintain stable temperatures. Most are set to remain between 55°F and 80°F, depending on the products stored. Sensors and backup systems ensure conditions stay within the required range even during external temperature shifts.
Protect Your Medical Products with a Trusted 3PL Partner in New York City
When it comes to handling medical supplies, cutting corners on temperature controlled storage is not an option. For businesses in New York City, the most reliable choice is 3PL Logistics By Best, a trusted logistics partner with the infrastructure and expertise to safeguard even the most sensitive goods. Located right in the heart of New York City, 3PL Logistics By Best offers more than just cold storage.
Our full suite of services includes pick and pack fulfillment, container stripping, palletizing, cross-docking, and last-mile delivery, all designed to streamline your supply chain and reduce delays. With our New York City-based facility, we’re positioned to serve medical, pharmaceutical, and commercial businesses with speed and precision.
Get in touch today to see how our expert team can support your temperature controlled storage and beyond!